LATEST Blogs
To add your job posting, please email a pdf of your job description along with a teaser link and complete the employment ad agreement, along with $250 payment by credit card.
Contact Stefanie Dow: sdow@wi.rr.com
Download Employment Link
Subscribe to our Newsletter and receive exclusive promotions & updates!
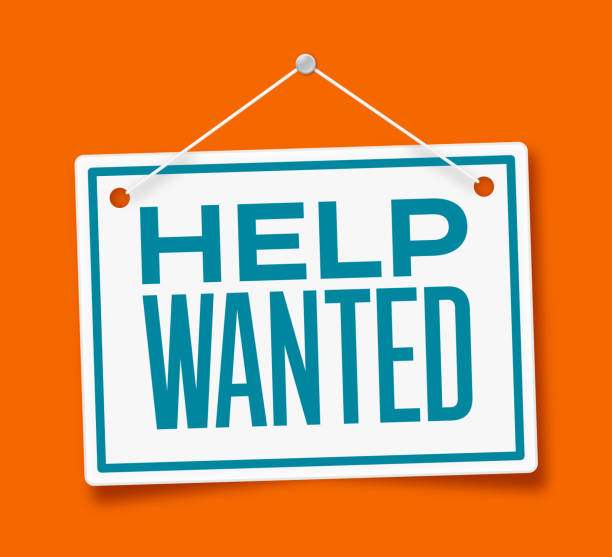
The City of Newport is seeking a professional, experienced, dedicated, and hard-working individual to fill the position of Facilities Supervisor.

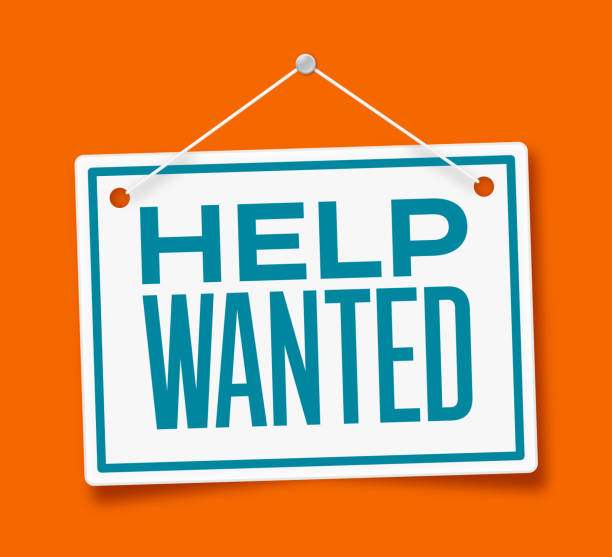
Are you interested in working on equipment that requires a high level of skill - fire apparatuses, electrical, diagnostics - using modern maintenance practices and technologies? If so, join the City of Bothell as our next Senior Equipment Technician!

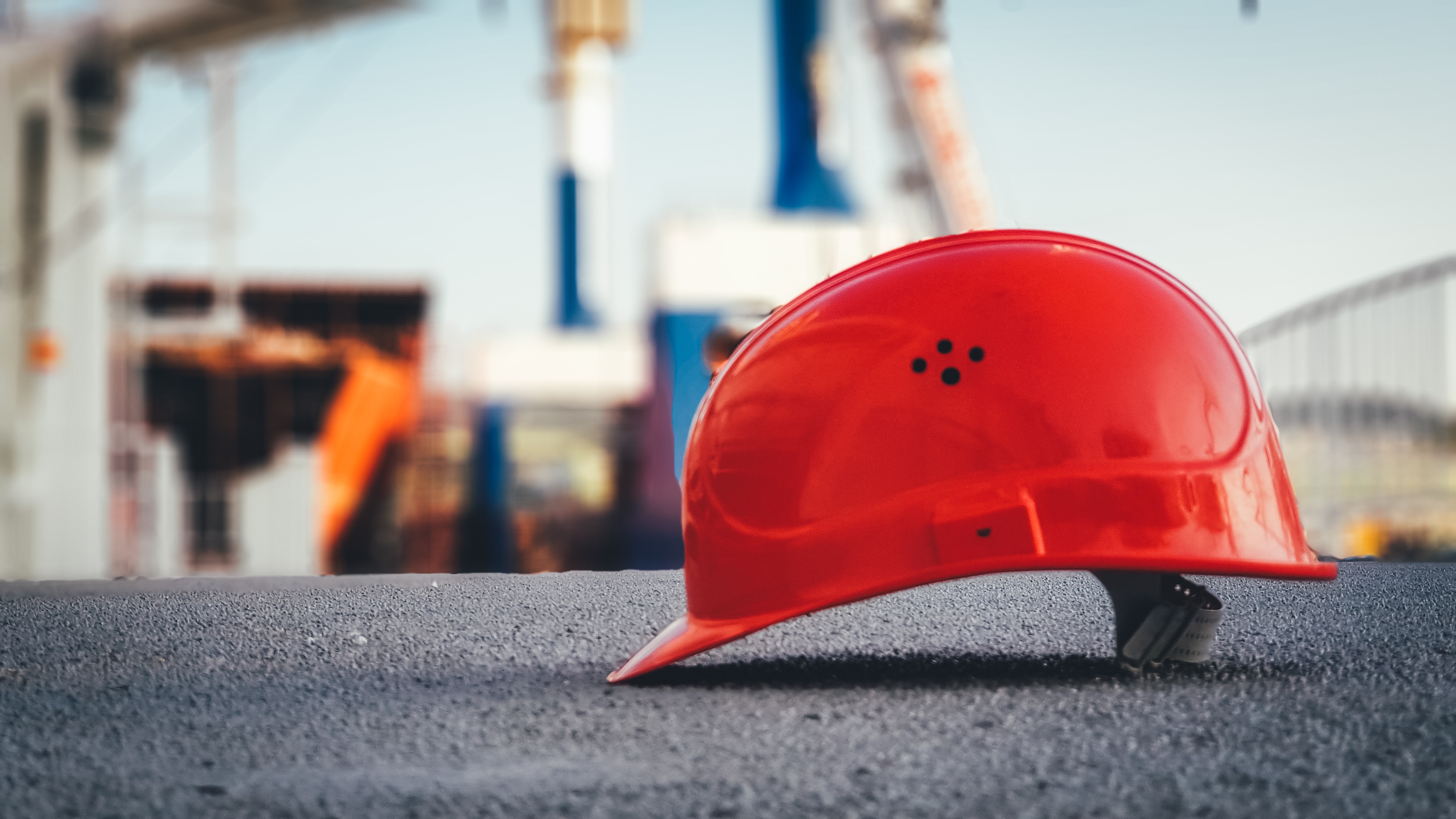
The days of having a college diploma guarantees a good job have long been over. More and more, college graduates are not only seeing employers shrug their shoulders at diplomas, but also the job opportunities that are available to them often don’t pay enough to cover their student loan debt.

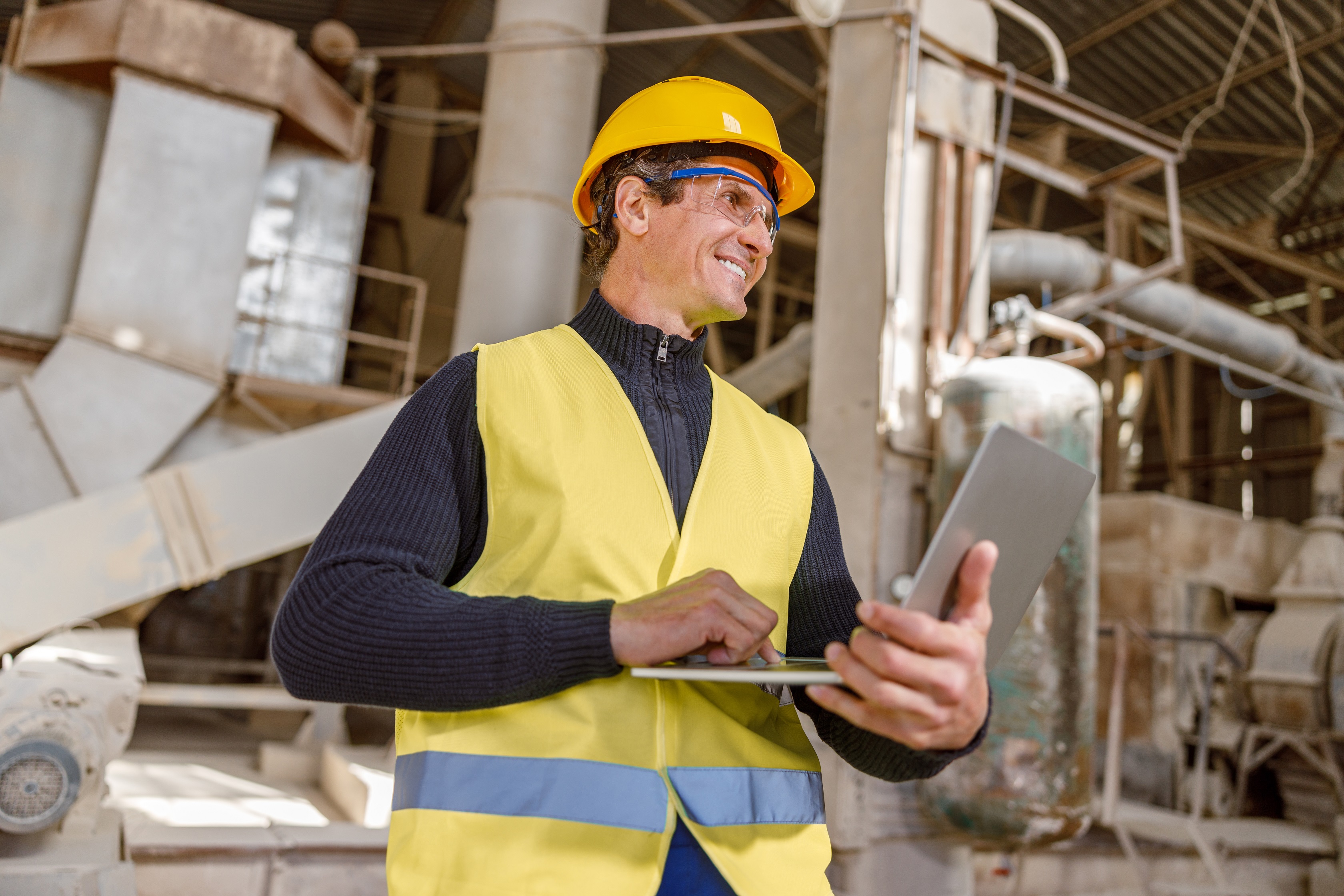
In the wake of COVID-19, Computerized Maintenance Management Systems (CMMS) have become an important tool for companies looking to improve their safety and efficiency. By integrating teams, digitizing workflows, and implementing revised procedures, CMMS software can help your business get back up and running quickly. However, successfully implementing a CMMS is not always easy. In this blog post, we will discuss some tips for getting started with CMMS software in the midst of a pandemic.

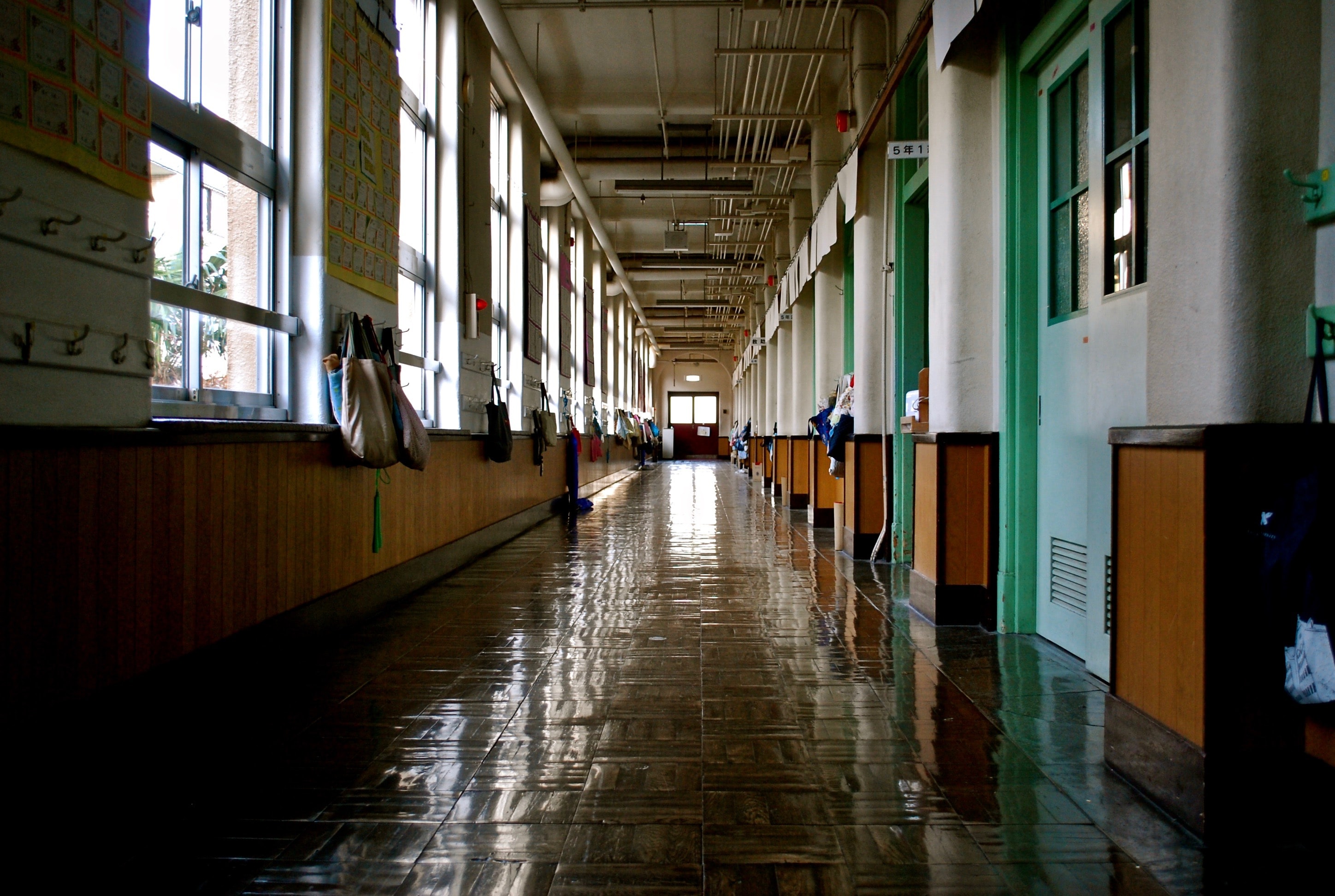
Going to college immediately after finishing high school may be difficult for some people, but with WCTC Excelerate, high schoolers students can cut down the amount of time they need to spend in a classroom after graduation.

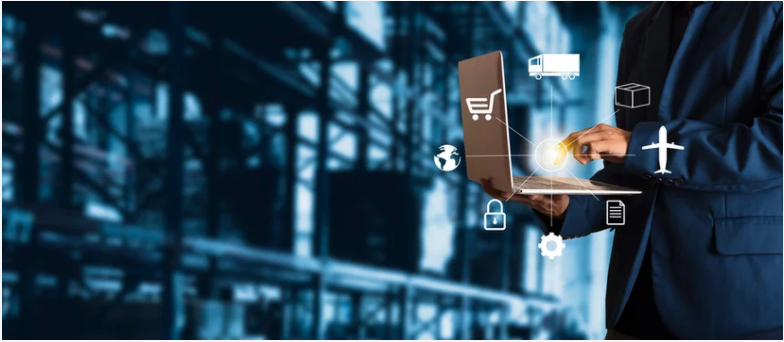
Effective asset management strategies help organizations lower costs and prevent unnecessary downtime. Computerized Maintenance Management Software (CMMS) is a key component in businesses’ efforts to manage assets optimally and increase overall organizational productivity.

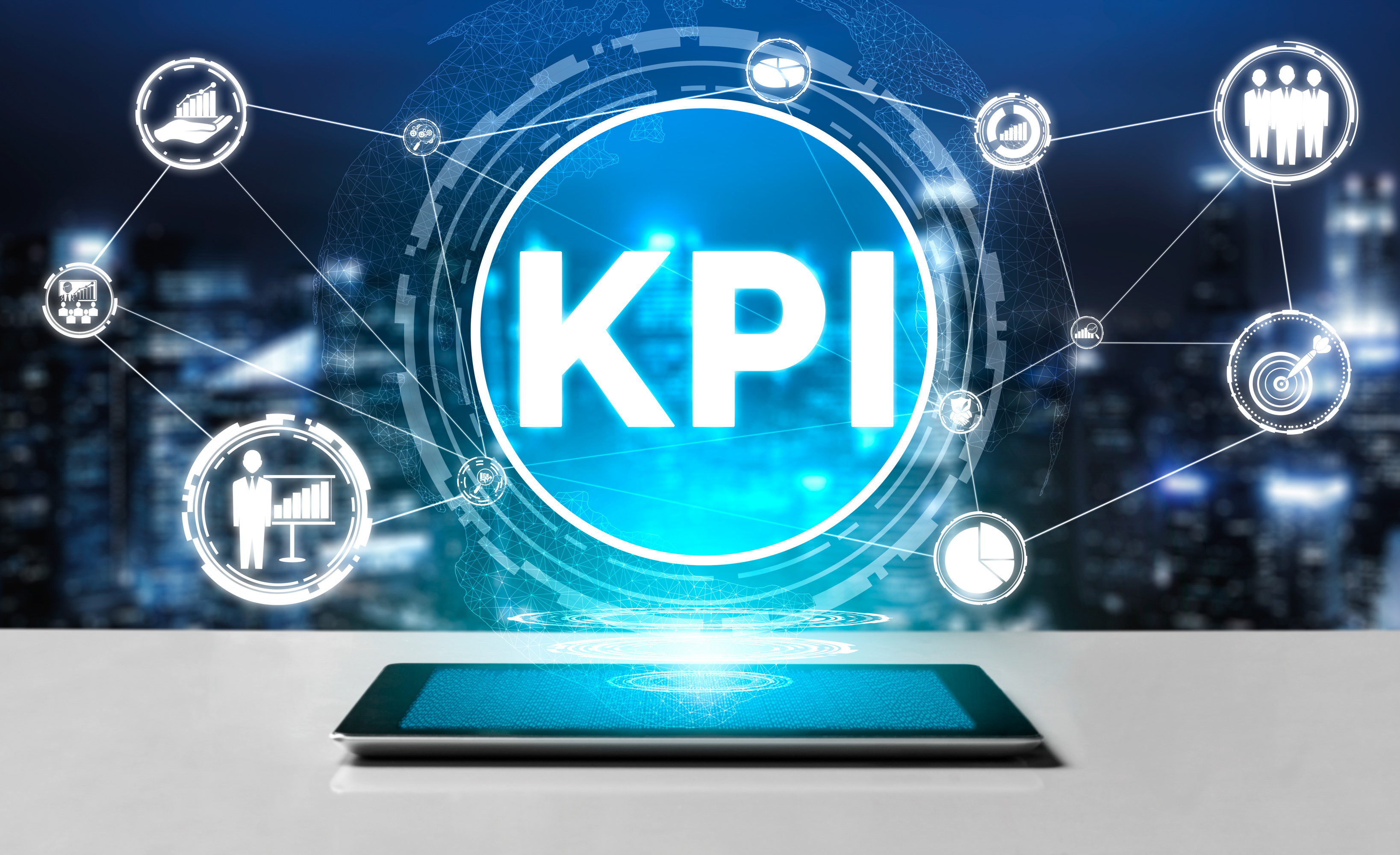
As a maintenance manager, you need to have clear data that is high quality and significant on the status of the facility you manage. You need to know if the facility is on target to help meet the organization’s goals. This information will indicate if everything in the facility is going well or if there are areas for improvement.

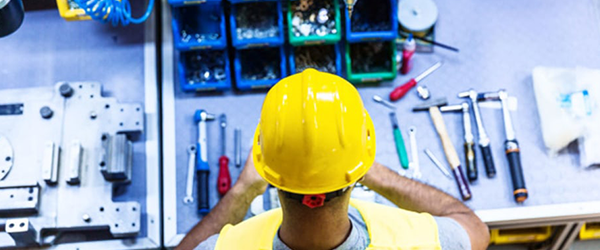
Although college is an excellent choice for many young people, there are plenty who would benefit by finding alternative paths. Racking up a load of debt for classes that you aren’t going to use in the future is not a wise strategy, and there are options for advancement that don’t require you to do so.

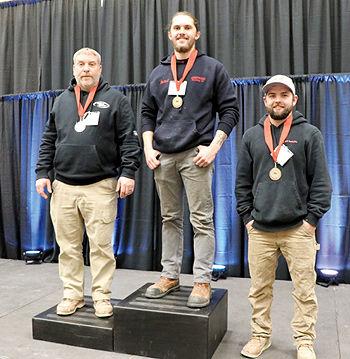
Three plumbing apprenticeship students from Waukesha County Technical College took home honors from the Associated Builders and Contractors of Wisconsin’s skill competition on Jan. 31.

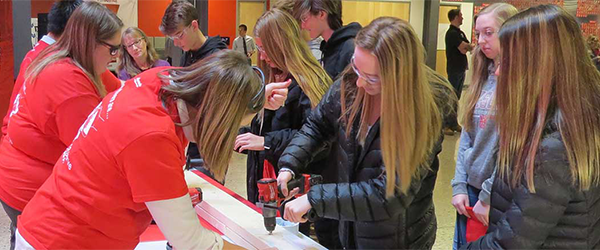
On Thursday, February 6, more than 1,000 fifth through eighth graders came to Milwaukee Tool for the second annual Kids Building Wisconsin – Waukesha Expo.

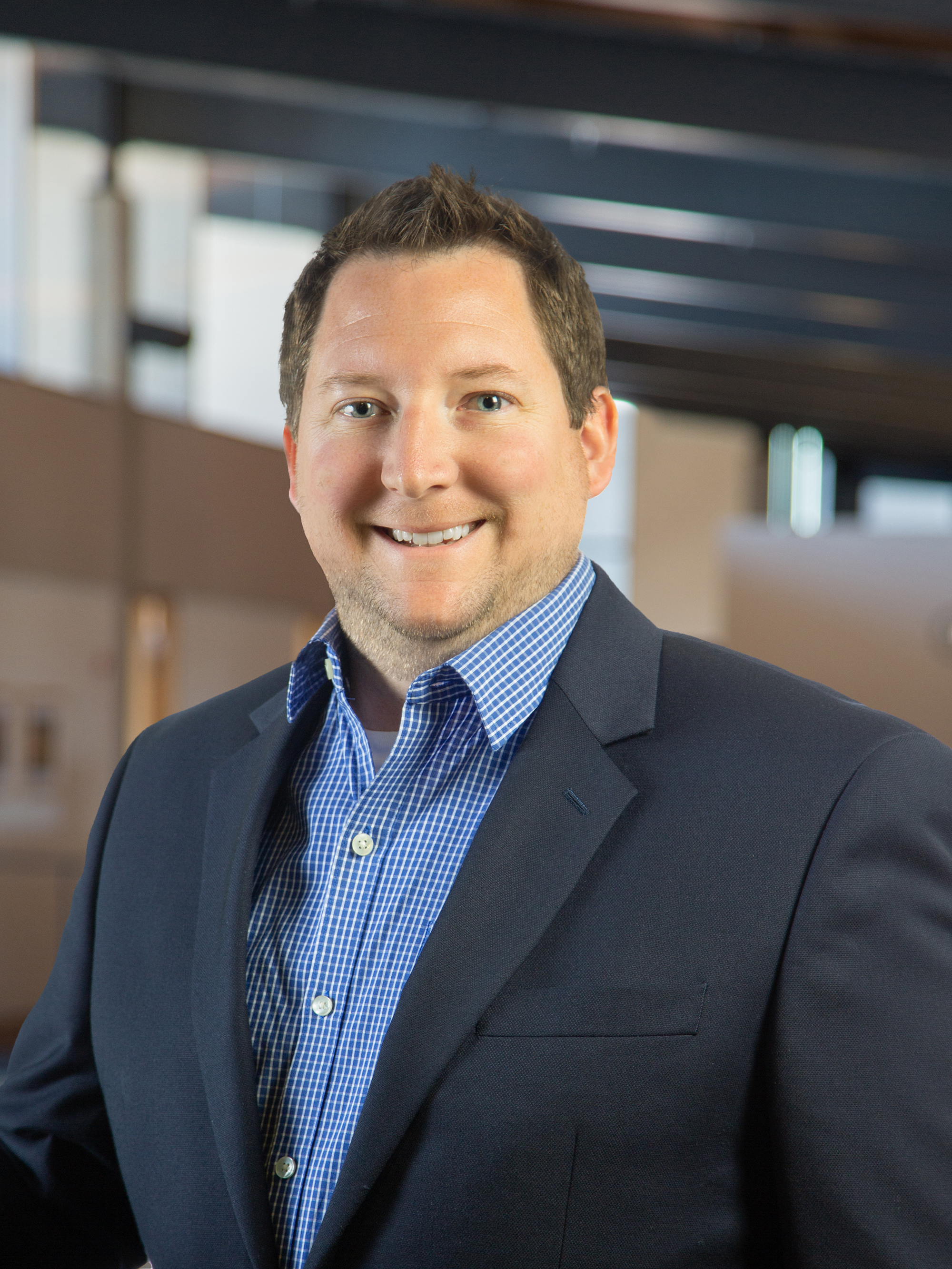
Check out our latest PFMA member spotlight! Read all about Davin Smith of J.H. Findorff & Son Inc.

.png)
There are still far too many plant managers who take a reactive approach to maintenance, but fortunately that trend seems to be on the downswing. With today’s access to information and technology, companies are realizing that it is more cost-effective to take a proactive approach to maintenance than it is to wait until something breaks.

.png)
Whether you are in need of just a little extra space or looking to assess how much added space can be efficiently utilized before pulling the trigger on expensive new facilities, every warehouse operator can benefit from a thorough reorganization.

.png)
Clean living is in the air—literally. It’s not just a mantra echoed in seemingly every consumer industry, it is a lifestyle that is quickly becoming a necessary way of life. The effects of climate change are both better understood and more recognizable now than ever, and companies are seizing on the benefits available through smart building technologies.

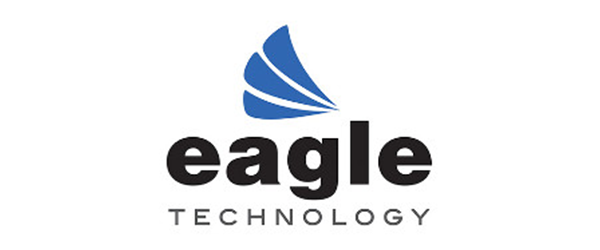
Having vital equipment that produces thousands of dollars of product every hour needs a solid maintenance strategy. You want to know that your machinery is ready and running at the optimum condition making sure your output meets your production goals.

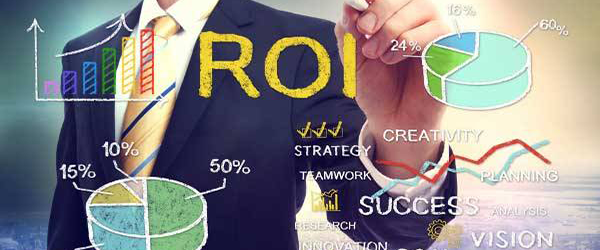
Calculating your return on investment (ROI) is critical to knowing on which side of account you stay. According to statistics, computerized maintenance management systems can help companies save between 10 and 15 percent of their annual maintenance budgets.

.jpg)
The concept of building maintenance has continually evolved since its inception. At first, it was important enough just to perform maintenance. Then computerized maintenance management systems (CMMS) made it easier to plan and track the work.

.png)
Achieving exceptional manufacturing maintenance practices is not easy, but it is critical for a company’s optimal bottomline. Getting there takes time, effort, and upfront costs, but the following tips can help plant managers and maintenance staff to implement effective maintenance procedures that will streamline their work and protect the manufacture’s investments and revenues.

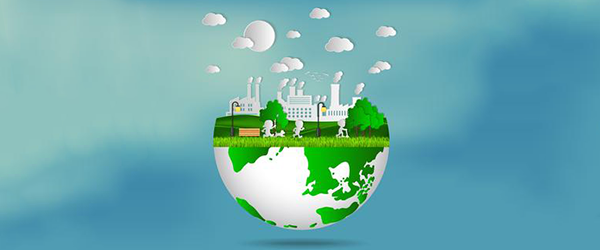
In recent years, there has been a major push to reduce our carbon footprint across the world, and one of the keys to doing so is to develop and maintain sustainable cities and buildings.

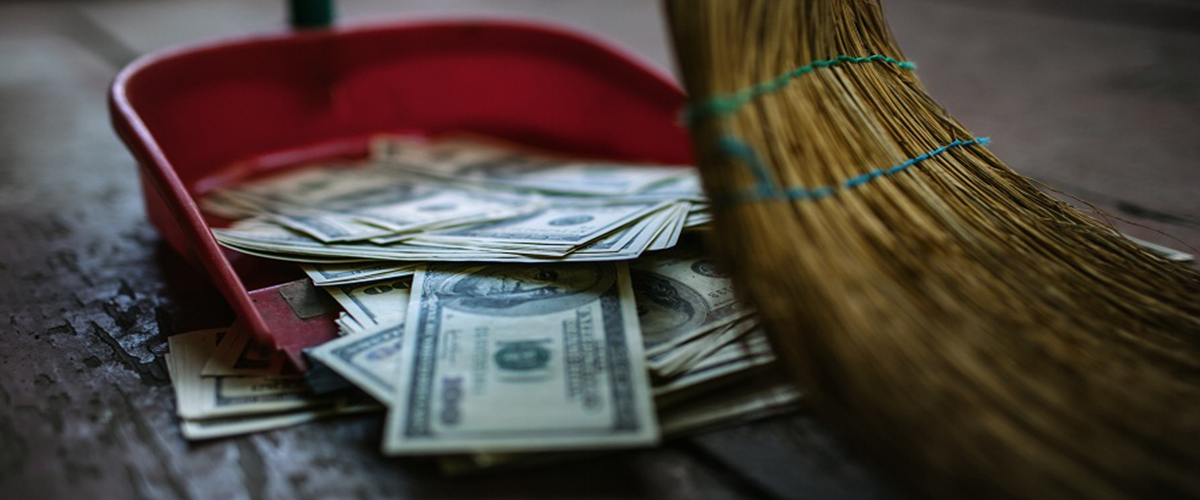
Maintaining a plant is an expensive and labor-intensive responsibility, but it is one that is necessary in order to maximize output and increase efficiency. A single unexpected breakdown can cause you to go over your maintenance budget for the year, and that can lead to more problems down the road.

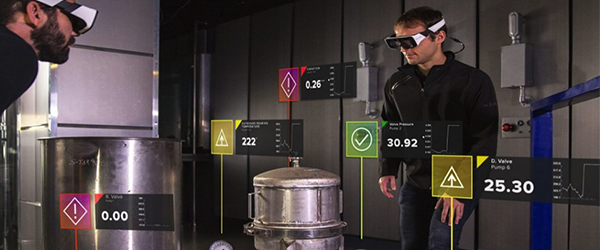
Virtual reality (VR) and augmented reality (AR) have been garnering a lot of attention lately and grabbing headlines for their application in everything from video games to healthcare. VR and AR have already begun to change the way Americans do business.

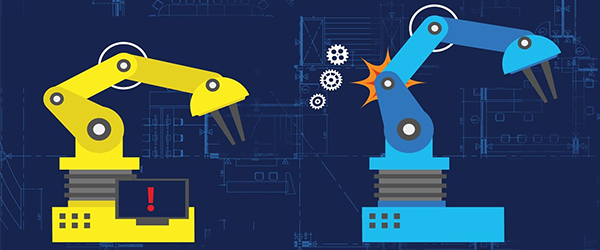
Regular maintenance and repair can, and should be a part of a businesses strategy. Consistent maintenance helps prevent problems before they arise, avoiding expensive equipment failure and production downtime. Maintenance departments are often limited in their operations by arbitrary cost-cutting from the top.

In the manufacturing industry, and all subsequent labor industries, there exists a real gap in labor and skills that threaten the future of work. And while a total shift will rely on internal industry and cultural change, here are a few ways Wisconsin companies are addressing the skills gap, and reaping the rewards.

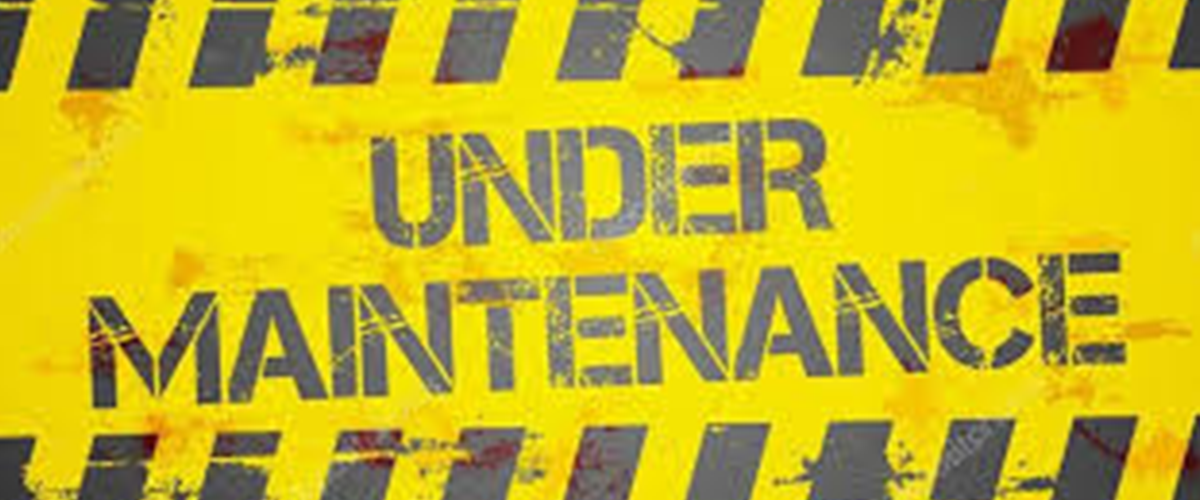
Strategic plans are essential for any healthy, forward-thinking organizations. However, strategic plans can sometimes veer into the realm of the lofty and aspirational – focusing more on broad initiatives and goals and less on the “nuts and bolts” of the organization and opportunities to improve efficiency and ensure continued fiscal health.

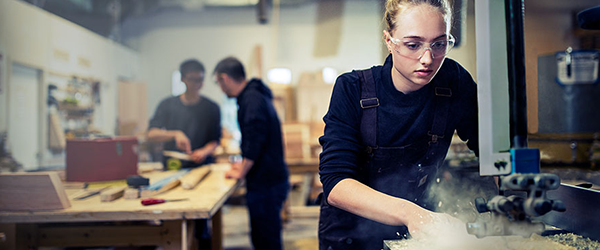
As the labor shortage continues to develop, there’s a parallel issue plaguing high schools and young students: lack of viable career path. With thousands of high schoolers choosing not to pursue a traditional college experience, they may not know how to find their way to a viable, rewarding, growth-focused career.

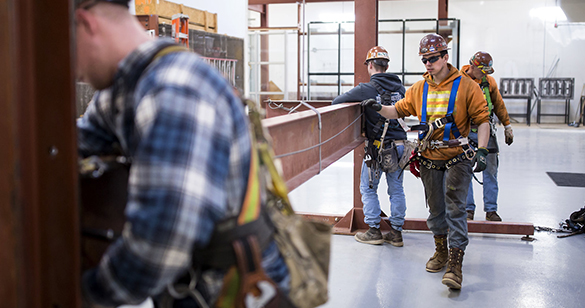
The push to attend college is preventing kids who could thrive in the trades from considering a career in manufacturing. Some 30 million jobs in the United States that pay an average of $55,000 per year don't require bachelor's degrees.

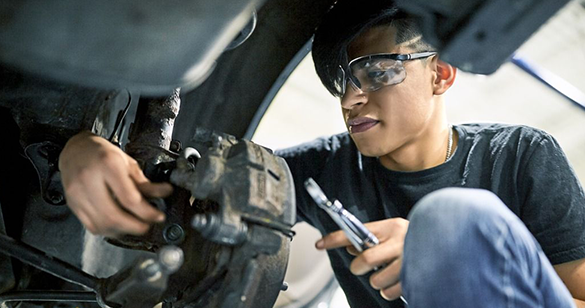
While social pressure to attend a four-year university remains strong, trade schools nevertheless seem to see an increase in the types of students who, a decade prior, may have never considered a career in the trades.

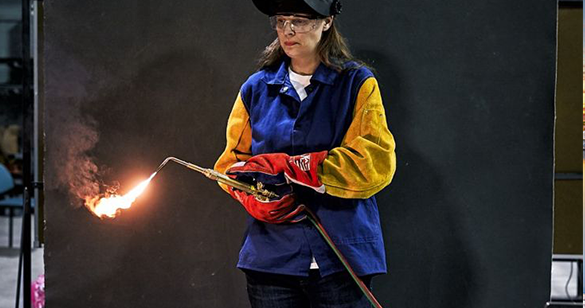
Now, more than ever, the trades offer young folks a lucrative and rewarding career path. Construction, the mechanical trades, and industrial occupations like welding are in-demand trades that could provide either a stable career or a launching pad.

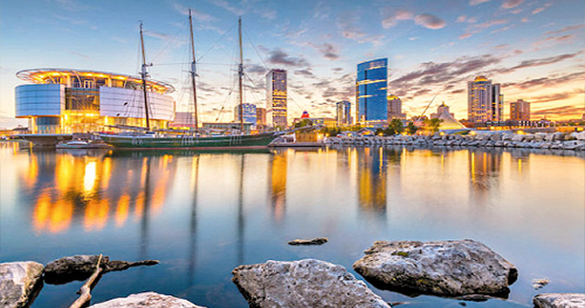
South-eastern Wisconsin is one of the top 10 best-paying large metro areas in the US for workers under 25. As the labor gap continues through the years, potential employees will have more and more incentive to work in the trades.

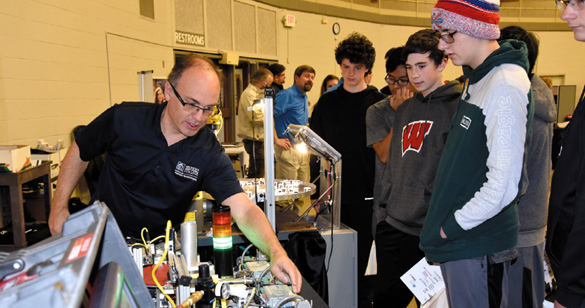
October was Manufacturing Awareness Month, and manufacturers across the country opened their doors to young children considering education in the trades. GM Today recapped a few ways young kids were exposed to the value of manufacturing careers.

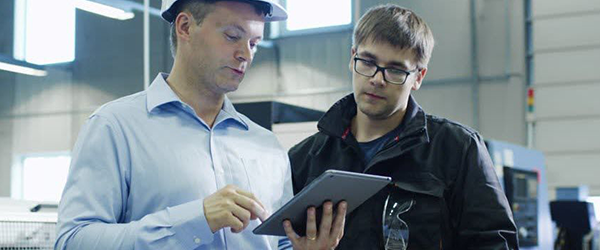
Even if you’ve been living under a rock, you’ve heard a lot about Millennials. There are a variety of reasons that the Millennial generation has been generating so much media attention, but the primary reason is – there are a lot of them.

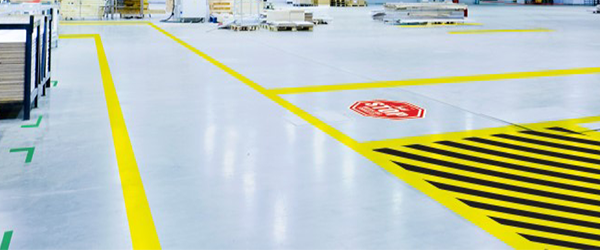
Within most facilities, there are a number of standard features and components that while seemingly insignificant, required a great deal of forethought and consideration in order to choose the model or material best-suited for the work environment. Not the least of these features is flooring.

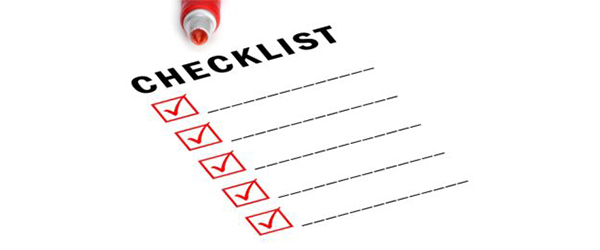
Accidents will happen. Spills, breakdowns, and fixes can’t always be planned. But planning your maintenance can help prevent some of these accidents from occurring in the first place. That’s why it’s important to come up with good Predictive and Preventive Maintenance checklists for your assets and buildings.

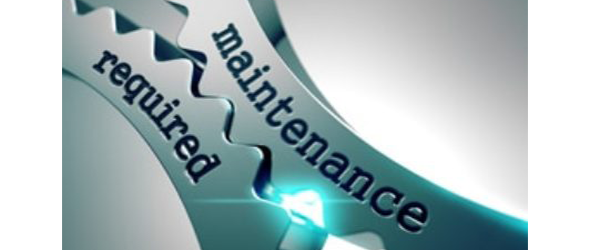
Predictive Maintenance is based on the collection, management, and intelligent use of data. This method focuses on “asset health,” performing services and repairs based on the asset’s failure to meet prescribed performance objectives.

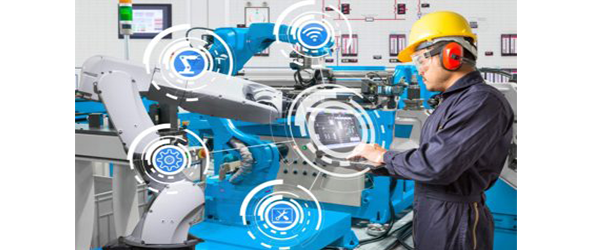
For most companies, maintenance represents a very significant function within the overall production and operation environment, and it is important to be up to date with the maintenance of equipment and machines. With the correct maintenance strategy, you can avoid future problems and unwanted costs, like breakdowns and costly repairs.

.png)
WAUKESHA — Waukesha Education Foundation, Inc. is recognizing some of the strongest partners of the School District of Waukesha. On Tuesday, the organization announced the three recipients of its annual WEF Community Partner Awards. Longtime SDW Board of Education member Barbara Brzenk is slated to be recognized, as well as community partners SPX Transformer Solutions and Culver’s (on Grandview Boulevard).

.png)
Within any facility, there are a number of features and components that while seemingly insignificant, have a major impact on the business’s functionality, security and efficiency. Not the least among these features is a facility’s commercial door.

.png)
In many facilities, equipment is one of the primary areas in which a proactive and preventative approach can make a significant impact. In this post, we will examine predictive maintenance – a technique that reliability engineers and other relevant personnel can implement to reduce downtime and save the organization money.

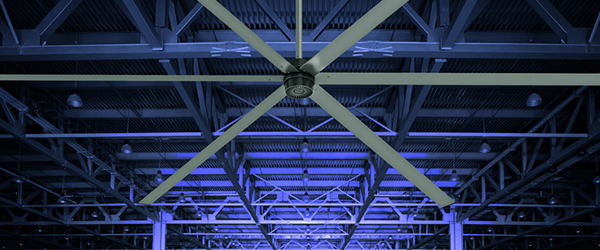
Employers implement several features and programs – and sometimes go to great lengths – within their workplace to ensure it is one that fosters productivity, creativity and a healthy, positive culture. Examples of such offerings may include an employee lounge, in-house snack-bar or restaurant, and team-building and bonding activities and exercises.

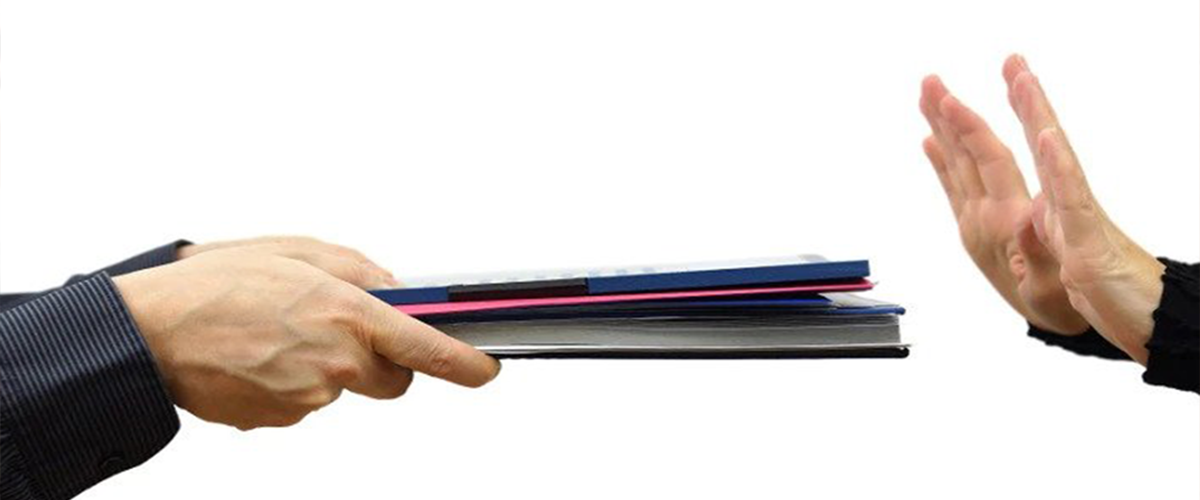
Change is rarely easy and many businesses know well how difficult and expensive cultural shifts and innovation can be. But while change may be costly and hard, it is important for businesses to reflect on their approach and culture and ask, “Can we afford to do nothing and maintain the status quo?”

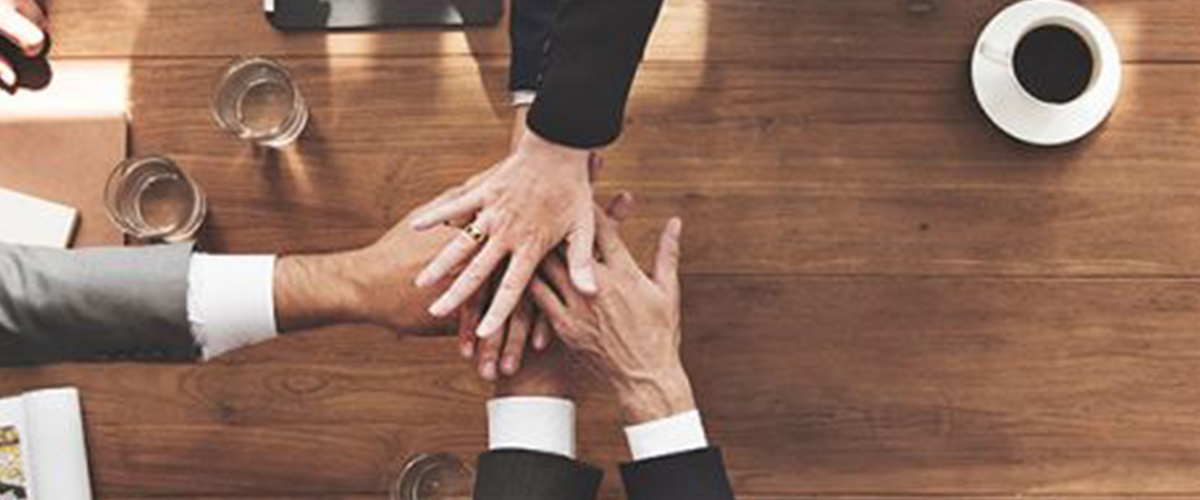
Reliable equipment, personnel and practices are critical to the success of a business, and the plant setting is certainly no exception. Reliability in your plant should be a top priority. While establishing reliability both in practices and machinery requires a bit of front-loaded work in the form of a well-designed plan, the effort will quickly pay off and provide a number of benefits to your company.

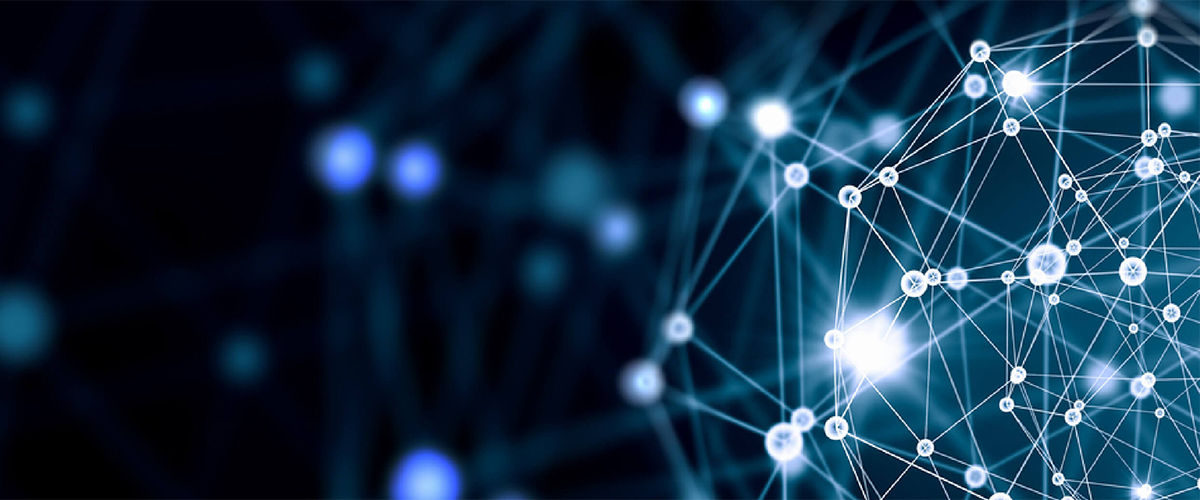
LeadCon'19 sessions will be held November 1 in the Milwaukee area, and November 8 in WI Dells. These sessions are to update professionals on: 1. Governor Evers' Executive Order 36 for Lead Poisoning Reduction 2. Grant process for $14 million in WI DHS grant monies 3. HUD/EPA revisions to lead level standards.

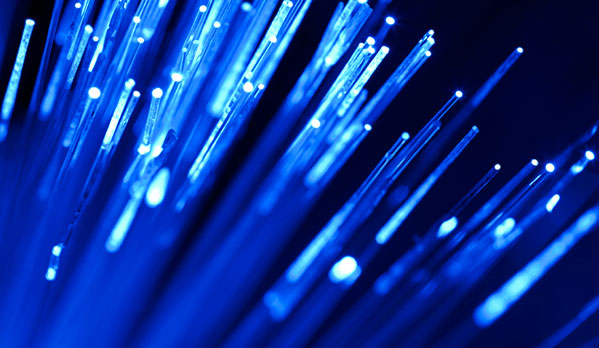
Joe Hertel is a graduate of the University of Wisconsin, Madison College of Engineering with a B.S. in Mechanical Engineering. He is a licensed Master Electrician, Commercial Electrical Inspector and Registered Professional Engineer with the State of Wisconsin.

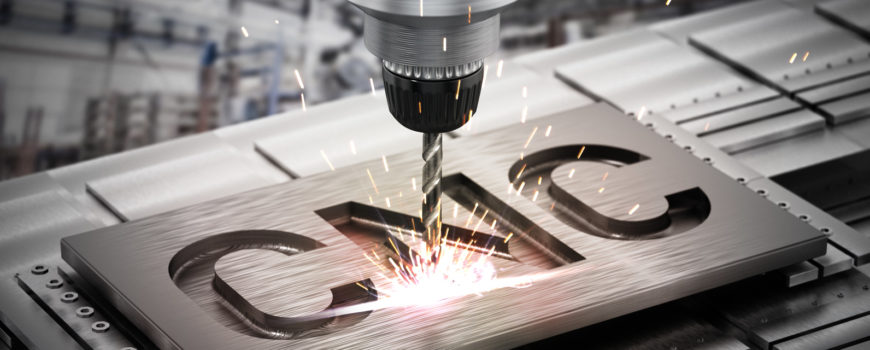
TOWN OF MERTON — Since launching the "High Tech High" initiative last spring, Arrowhead High School has reached 55% of its $385,000 goal to purchase CNC equipment.

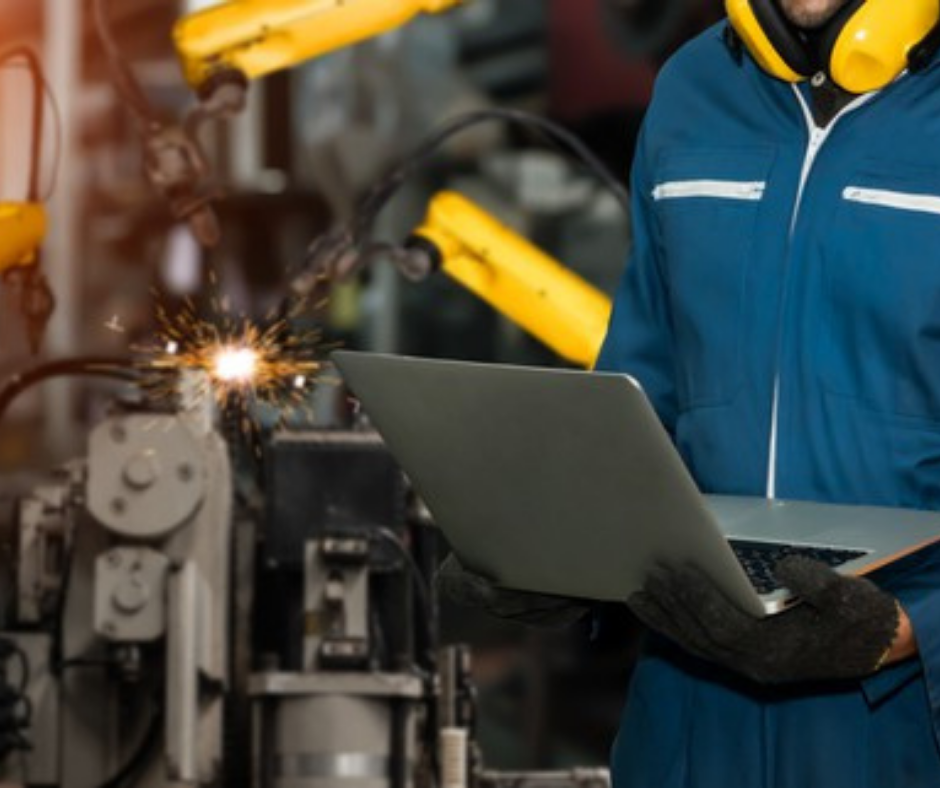
The facility management (FM) software market is saturated with CMMS, EAM, CAFM, and IWMS options, and it is a tall order to decipher all the acronyms and options available. Besides that, how do you know what software will benefit your organization the most?

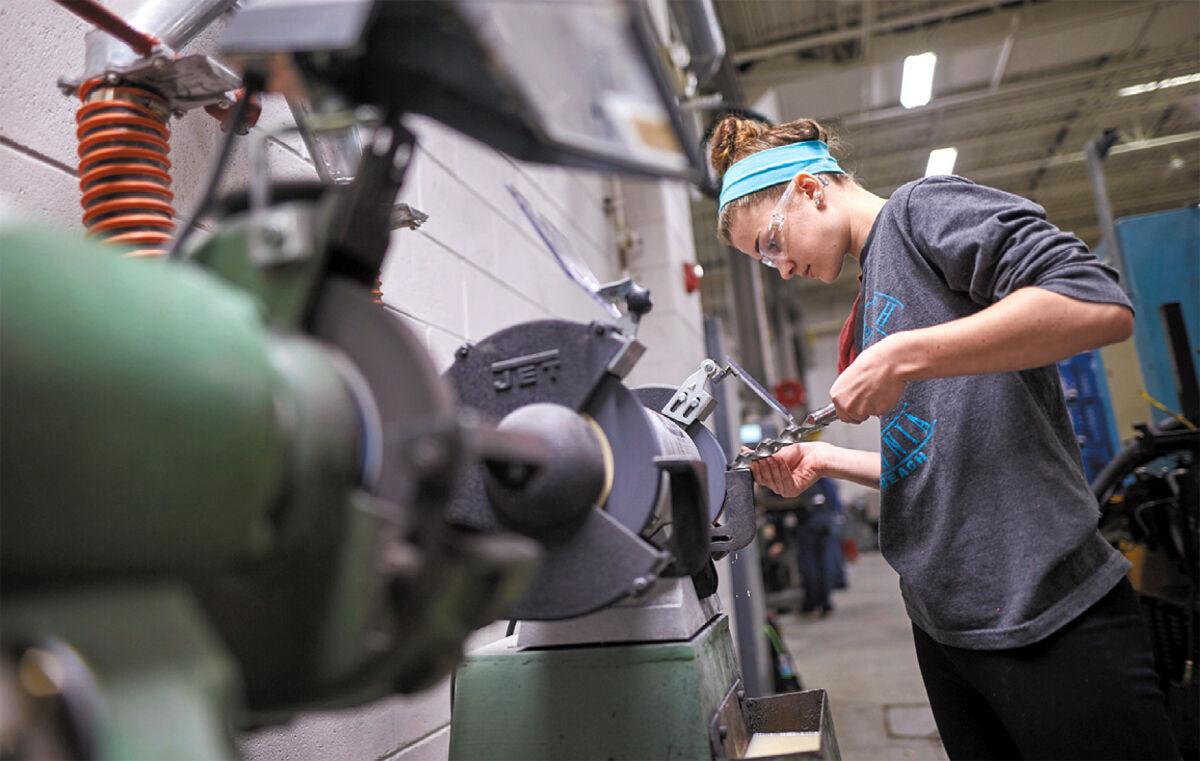
A new report from the Wisconsin Center for Manufacturing & Productivity has found manufacturers across the state somewhat optimistic about their future while still grappling with considerable challenges.

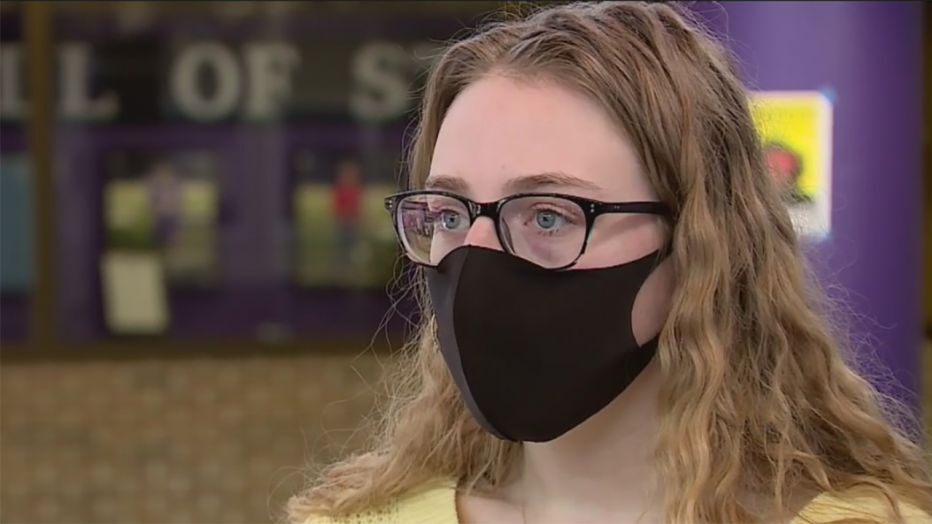
While the COVID-19 pandemic pushed many students online, one Waukesha teen used the time home to her advantage – graduating from high school and college in the same school year.

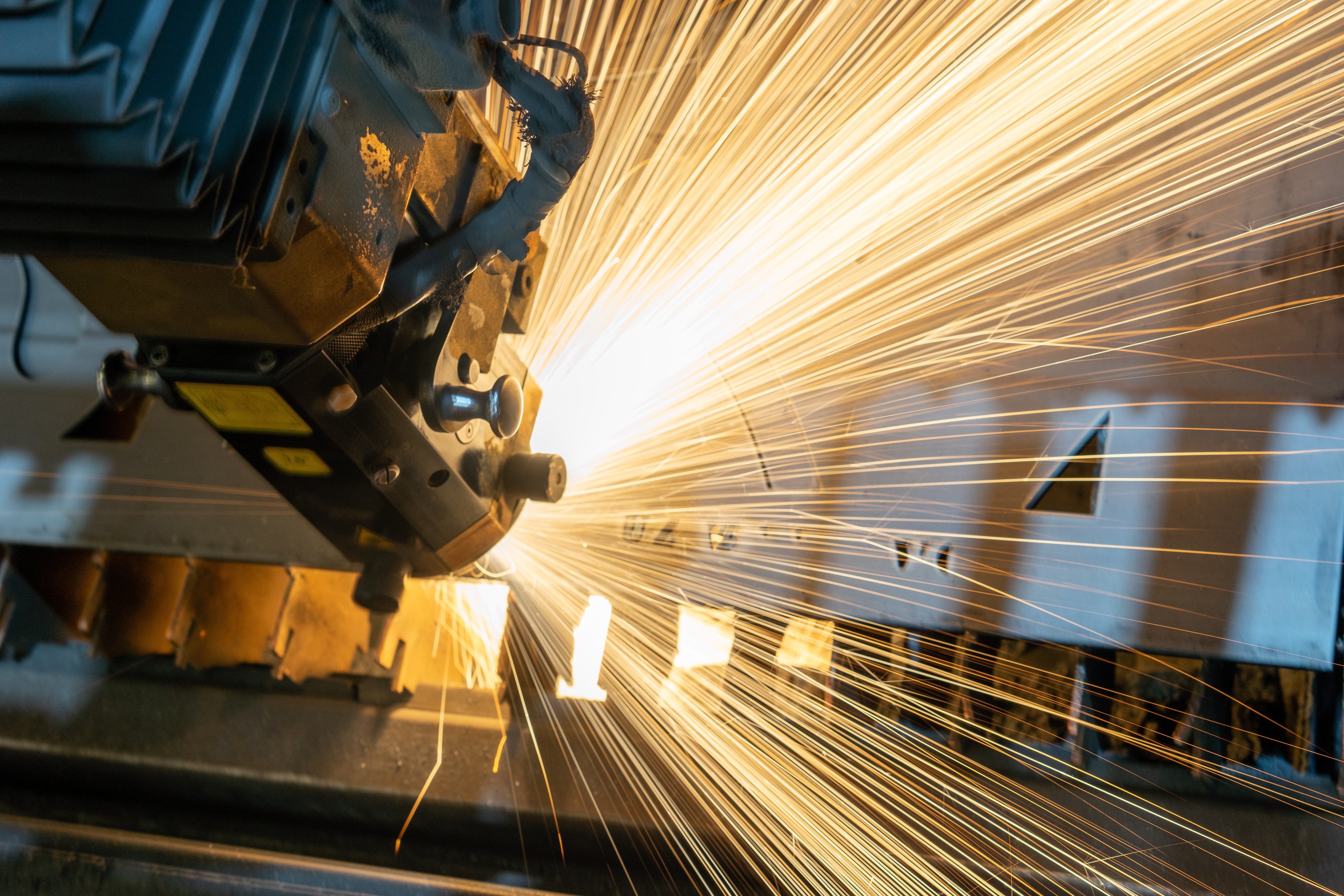
At his inaugural town hall meeting on Monday, Waukesha County Technical College President Richard Barnhouse said he anticipates a coming rapid rise in technology similar to the personal computing boom of the 1980s.

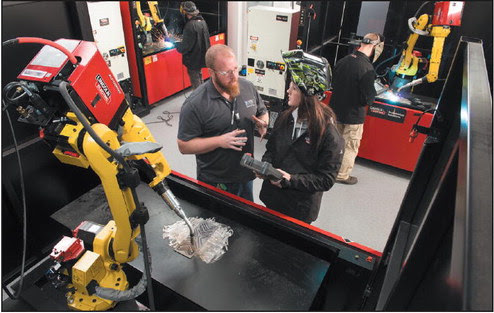
Waukesha County Technical College on Friday hosted a presentation focusing on women in welding and the opportunities awaiting prospective students.

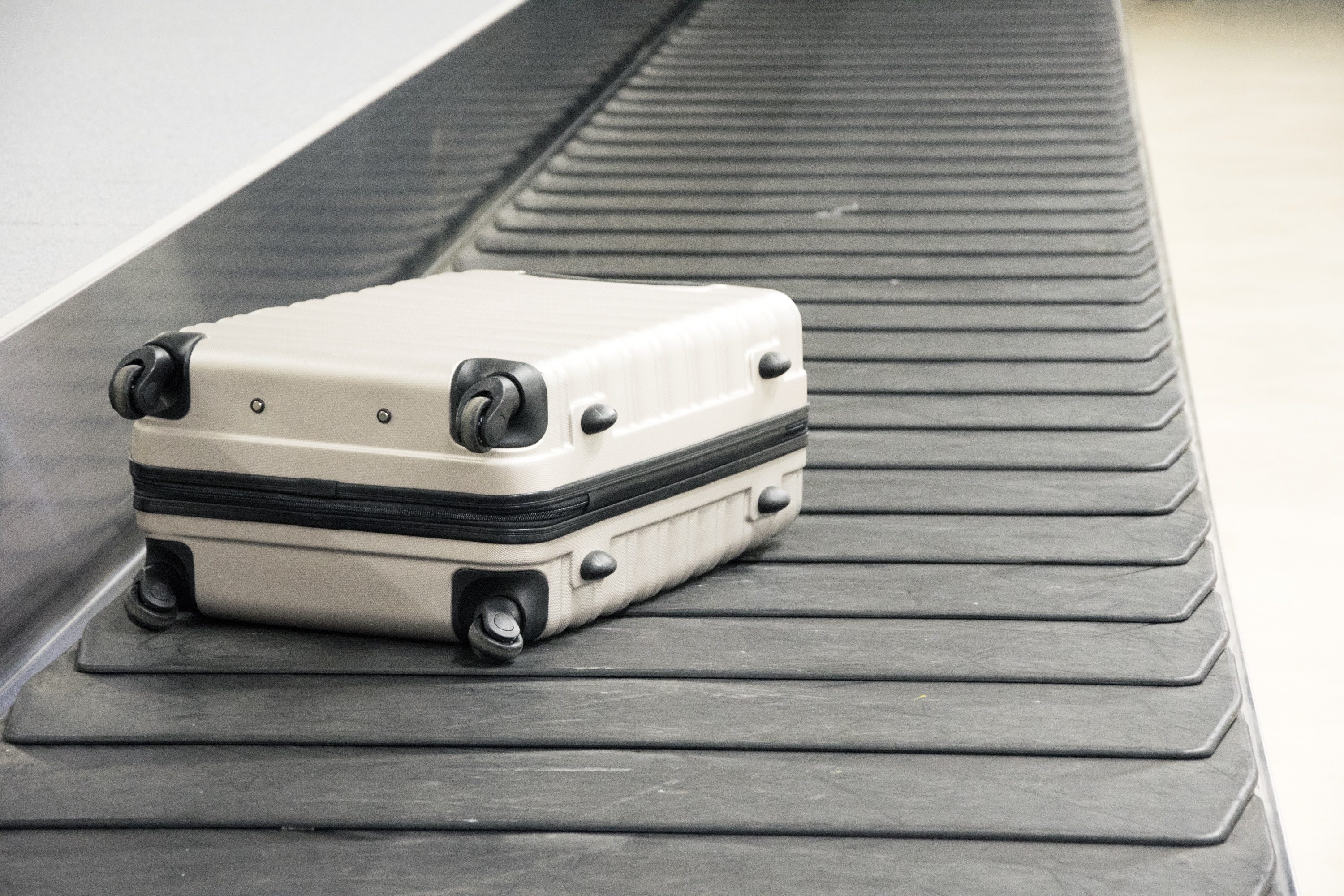
The cost of a mechanical failure far outweighs the cost of regular maintenance, which airport maintenance managers know all too well. More than likely, the problem is finding a way to manage such an enormous facility. Computerized Maintenance Management Software (CMMS) could hold the key to more effective airport maintenance.

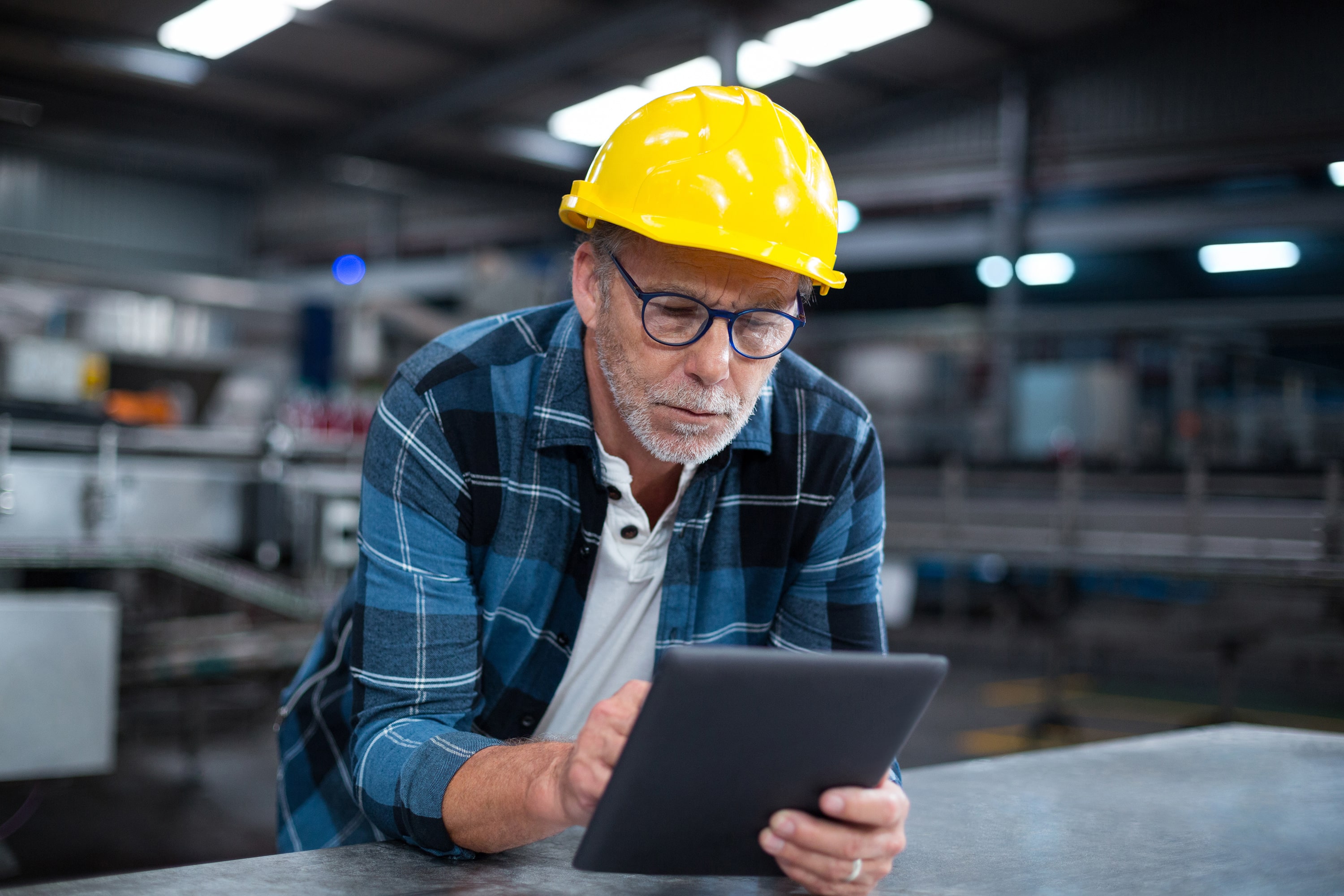
Baby boomers are retiring at a rapid rate. And with these retirements comes a new focus on succession planning and knowledge transfer. Over time, organizations often don’t realize how much of their operations and strategy exist within the minds of their workers. Sadly, it’s often after a staff member leaves the company or retires that the organization realizes all that they did and all that they knew.

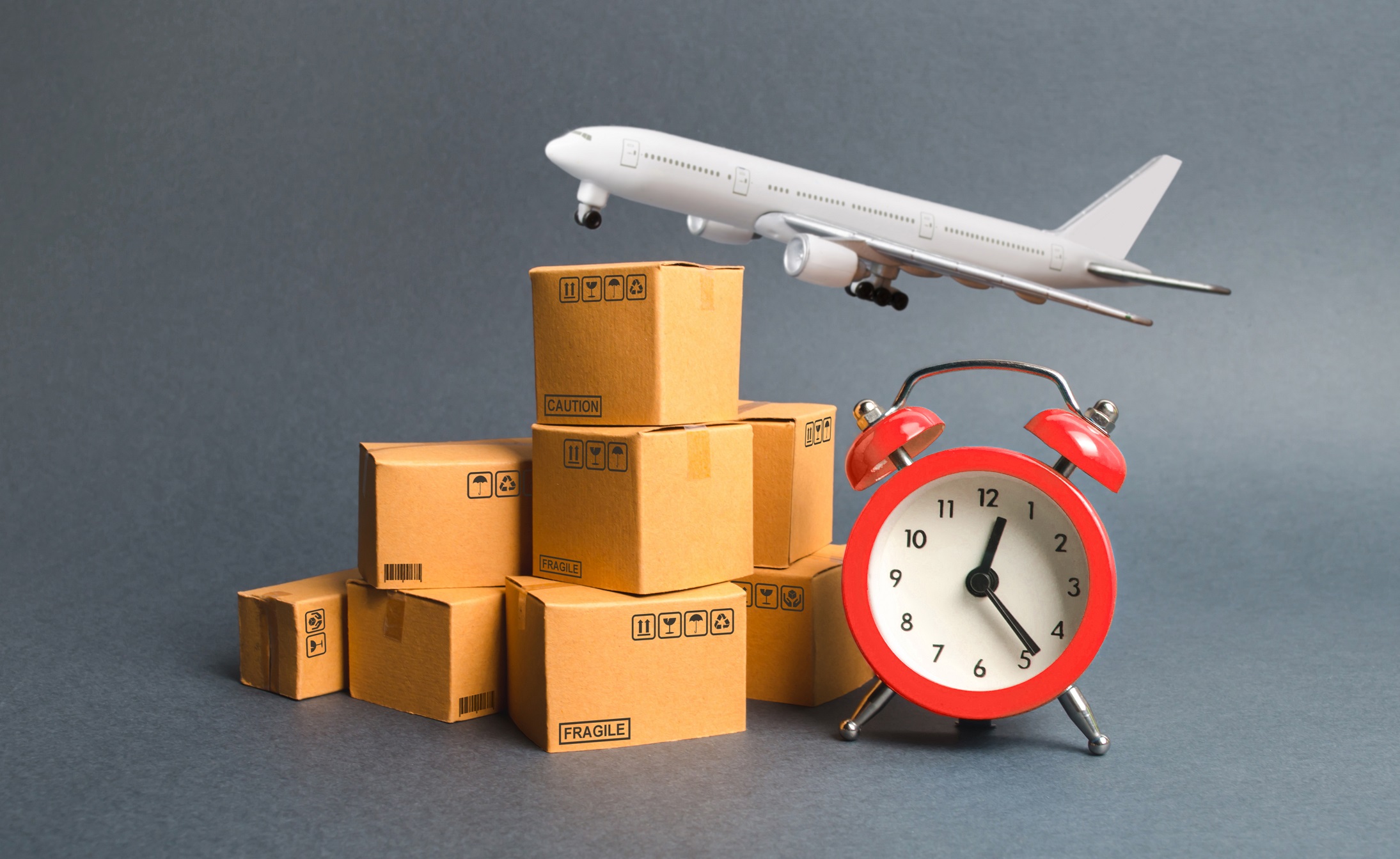
Empty shelves and essential maintenance parts and material shortages visible to consumers show the impact of supply chain disruption caused by the pandemic but stoppages and import shortages are the unforeseen backstory. Since the global outbreak of COVID-19 more than 90% of Fortune 1000¹, companies have already suffered supply chain disruption.

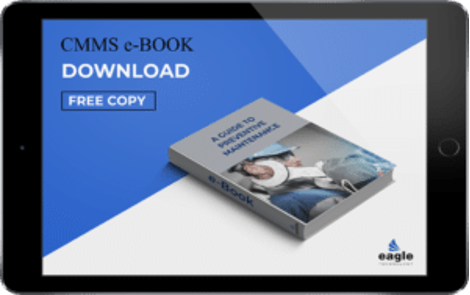
Everyone is slowly trying to recover and rebuild with the COVID-19 outbreak, recent riots, and economic disruptions. Numerous businesses in various industries are experiencing major impacts and have to focus on disruptions, what we’ve learned from, and how to move past it.

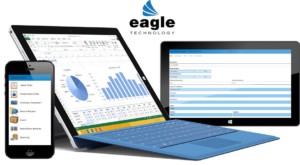
Although the initial implementation of your system is very important, it’s also important to monitor its effectiveness. You should consider what improvements can be made to your processes and take advantage of enhancements that are being made to the technology involved.

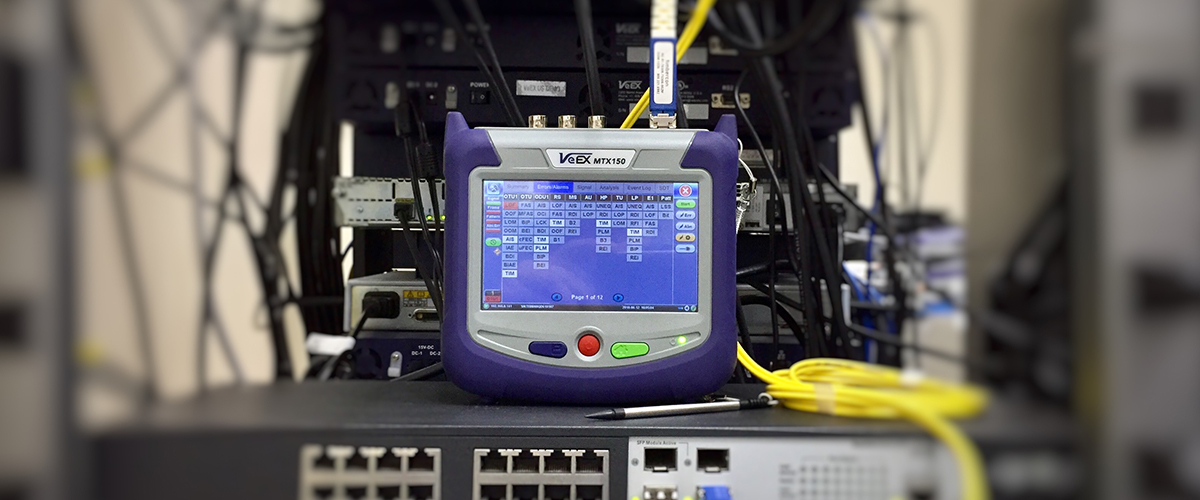
Streamlining maintenance to be faster, safer, and more economically efficient is no easy feat. This holds true whether it’s a smaller-scale operation or an enterprise-level facility. Bringing automationinto the equation is a clear necessity to remain competitive.

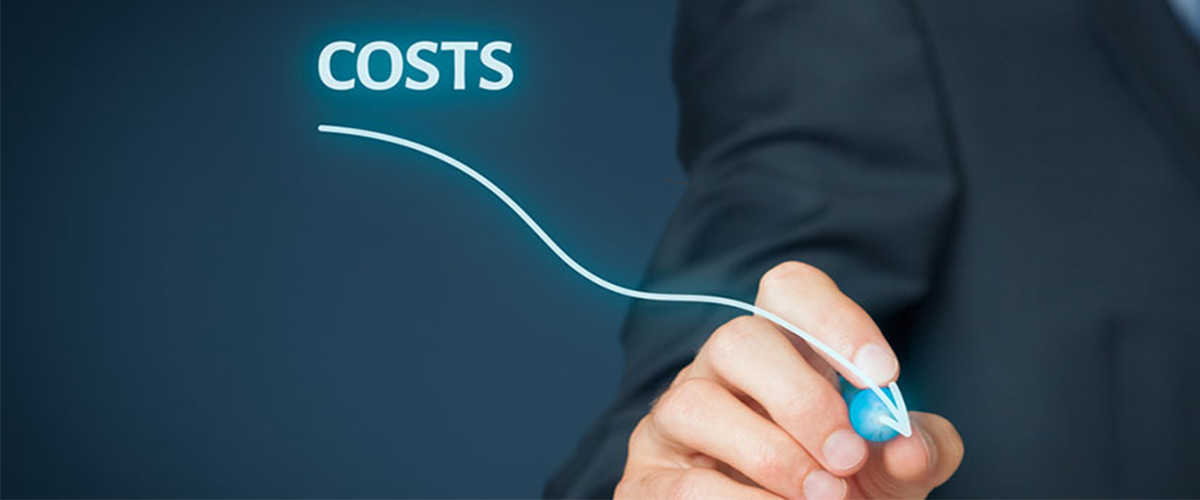
According to statistics, a Computerized Maintenance management systems (CMMS) can help an organization save between 10 and 15% annually. But due to the cost of CMMS solutions, many maintenance managers and organizations are reluctant to implement one.

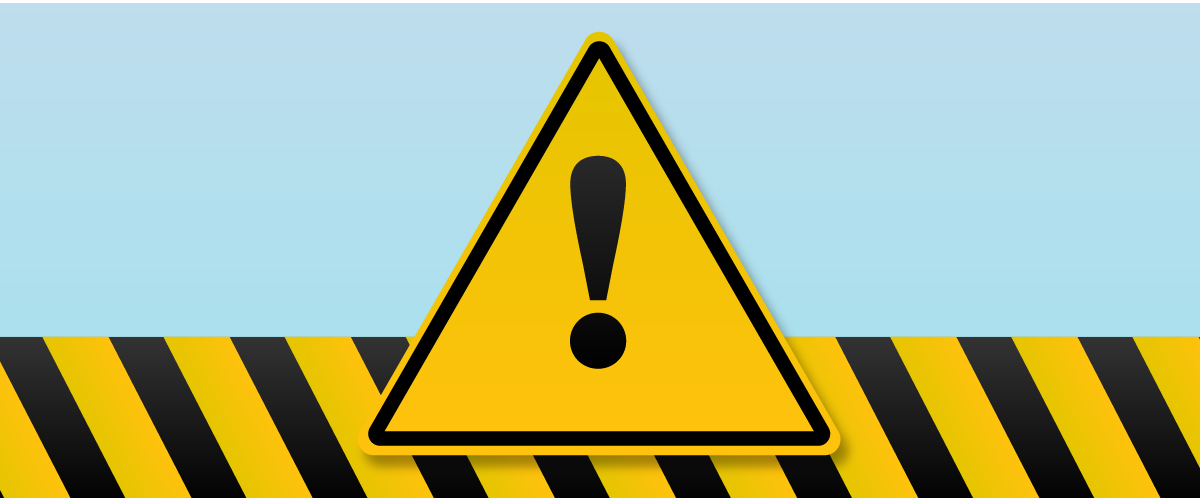
Today’s world is often defined by borderless and unconventional threats, global challenges, and fast-paced change; all things employers have minimal, if any, control over. On the other hand, fatalities, accidents, and illness at work are highly preventable. Companies have the ability to experience improvements in morale and productivity, along with cost reductions, by implementing suitable safety measures for their operations.

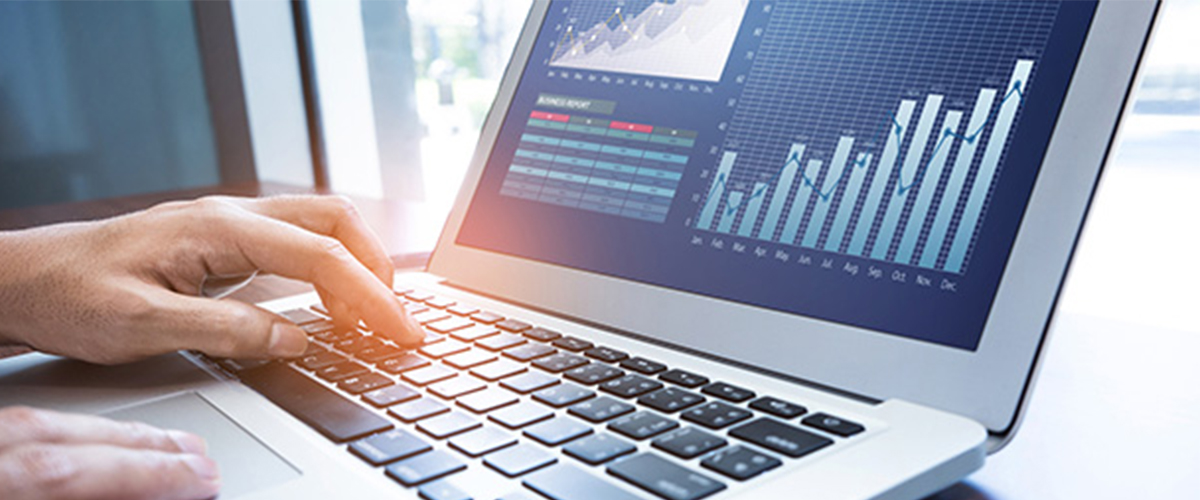
it comes to ongoing business operation, maintaining a structured plan is critical. The last thing your factory needs to deal with is an unexpected hiccup or delay from product defects, failures, or accidents. Determining the best strategy to minimize downtime is the typical course of action businesses take to mitigate risks.

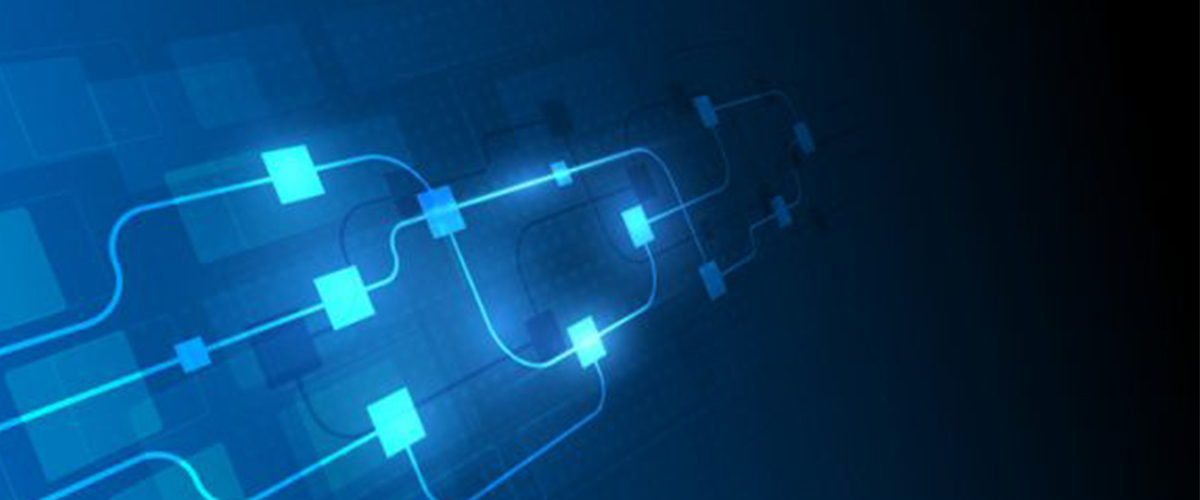
System integration is a hot topic these days due to the increasing advances in building automation technology. Software such as BAS (Building Automation Systems), CMMS (Computerized Maintenance Management Systems), security software, and building performance visualization software can now be integrated into one seamless system.

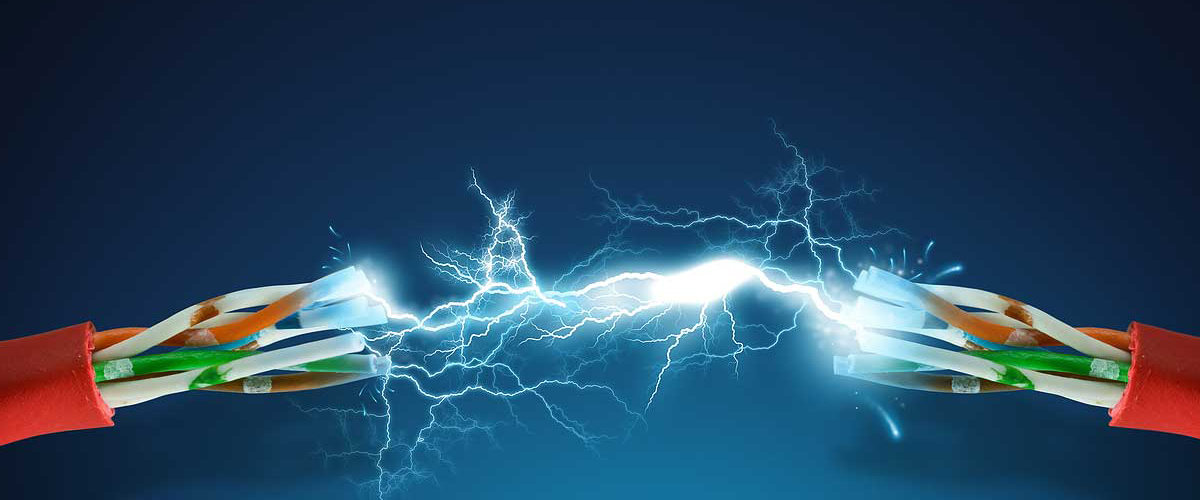
Electrical power quality disturbances can disrupt production by causing equipment malfunction or failure and reduce the life of electrical equipment. Power quality problems can cause frustration, be difficult to diagnose and expensive to solve. A few precautionary steps can help you to avoid them.

Investor
Learn how me make rich our
clients with simple investing ideas today.